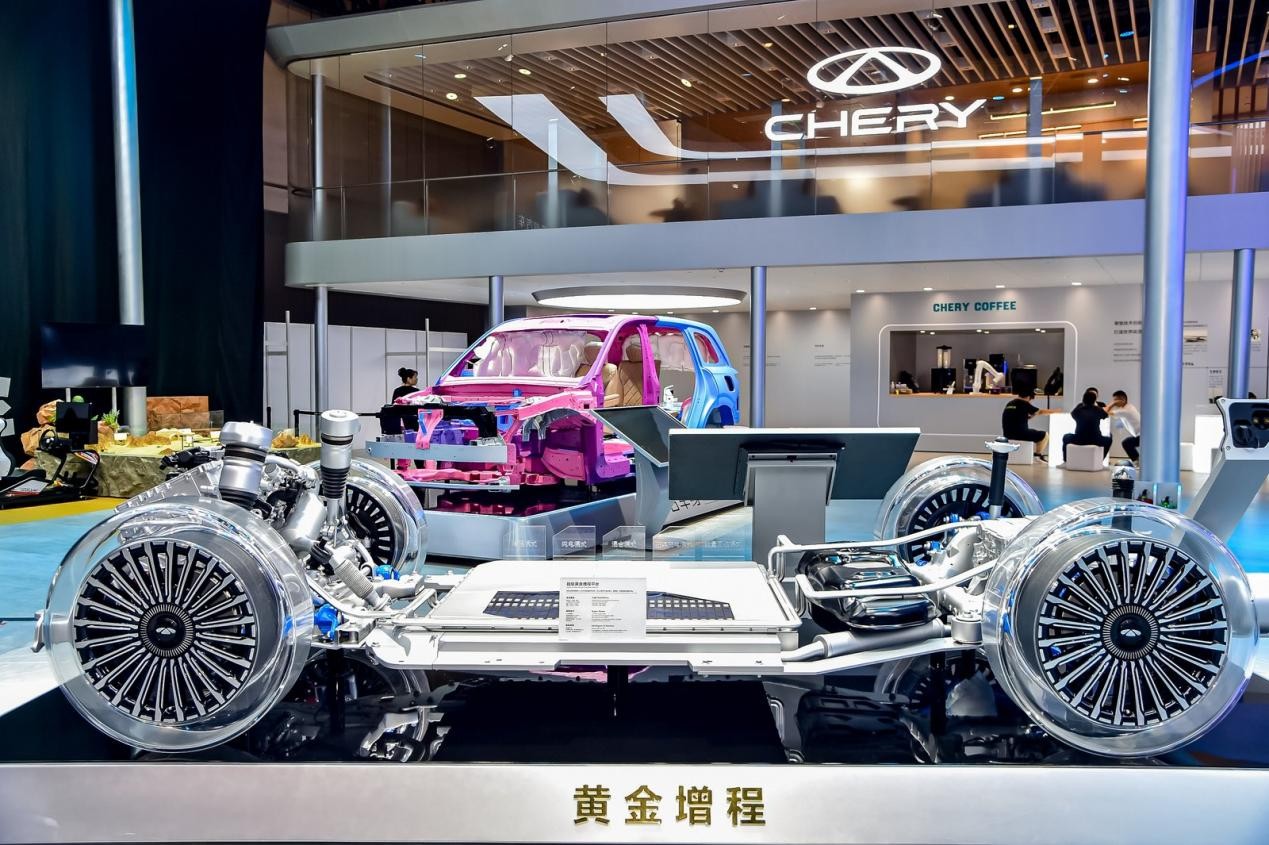
四大品牌集结, 奇瑞集31款重磅车型登陆成都车展
来源:汽车商业评论(汽车商业评论)2023-07-23 09:23
数字时代是继农耕时代工业化时代之后的一种全新的社会发展形态。
随着云计算、大数据、人工智能、物联网、区块链等新一代信息通信技术的发展和广泛应用,数字化正以不可逆的趋势改变着人类社会。
数字化时代的到来,为企业赋予了新动能,提供了进入新赛道及弯道超车的机会。
宏观政策的引领,数字经济的发展,用户需求的改变,数字技术的发展进一步加速了数字化转型发展的步伐。
面对时代的挑战和变革,2023年7月17日到18日,2023中国一汽第三届先进制造技术“旗智·iM”高端论坛在长春举办。
论坛上,中国一汽工程技术部(工艺工程院)总经理宋志勇以《创新驱动、数智赋能——打造新一代智慧工厂》为题,讲述了中国一汽如何将业务重构下的数字化建设作为实现战略转型的核心要素,打响了数字化转型升级的攻坚战,通过全面数字化建设,打造高效、精益、协同的企业运营,推动中国一汽实现高质量的发展。
中国一汽制造领域转型方向是打造基于智慧运营和智慧产线的智慧工厂,智慧运营和智慧产线技术架构的创建,实现了从产品定义工厂向服务定义工厂的转变,实现了从直线型流程决策向多组织协同决策的转变。
众所周知,单纯的满足产品投放,多车型混线生产的工厂设计理念,已经远远满足不了高效、精益的工厂制造运营的需求,远远满足不了市场的快速变化,用户个性化的急迫需求。
为此,中国一汽开启了打造智慧工厂的数字探索。聚焦智慧智慧工厂建设的愿景目标,我们识别了内部工艺工程师、上下游业务对象、终端消费者三大用户群,提出了工厂设计、高效协同、产线设计、低碳智能、制造运营、数字决策、用户体验、愉悦乐享的价值主张,并确立了灯塔目标,为打造世界一流的智慧工厂明确了方向。
同时中国一汽将现有的设计和运营业务解构成最小业务单元,并进行数字化治理,实现制造业务的沉淀和知识的复用。通过建立工作台,实现角色任务的驱动和业务流程在线化的管理,通过能力中心和能力组件的开发,实现设计和运营数据的可视化和分析应用。伴随着能力组件的不断迭代和完善,最终实现能力组件为业务赋能支撑工厂构建越来越智慧的制造运营应用架构的生长模式。
在智慧运营方面,基于产品诞生流程,IPD和订单交付流程OTD进行业务单元模型标准化的建设。目前,中国一汽基于生产、设备、工艺、质量、能源、安全等7个维度,进行了业务数字化的规则,业务流程数字化和业务对象数字化的业务重构,识别高价值点,进行面向服务的智慧场景建设。具体已经规划了工程仿真、设备运维、能源监控、线体调试等50余项业务场景,并逐项落地实施。
在智慧产线方面,中国一汽以提升制造效率,提升产品质量,降低制造成本为核心运营目标,采用国内先进的工业互联网平台,以智能化产线和装备为载体,对整车制造过程的数据进行全量、全要素的采集,通过数据建模、数据分析、AI算法等手段支撑数字化场景应用,实现整车从零部件到下线全过程的数字孪生,完成从传统制造向高端自动、精益、灵活、数字互联、持续学习的智慧制造的转变。
红旗新一代智慧工厂,打造人机高效协同的智慧工厂模式,实现人在管理和决策过程中有足量的高针对性的基础数据支撑,同时实现计算机具备人的思维,对产线及运营进行智慧管理及决策。
智慧产线以先进智能的装备和产线为硬件基础,以先进智能的技术手段为支撑,为智慧运营提供高度适用的知识和数据。通过智慧工艺、智慧生产、智慧质量、智慧能源、智慧安全、智慧维护等应用场景,实现智慧产线与智慧运营的深度融合。通过各个能力中心实现人与智慧工厂的交互,最终构建人机高效协同的智慧工厂。
为此,中国一汽在智慧工厂建设过程中开发了多个典型场景。
第一个是智慧工艺典型场景,冲压端拾器的自动设计,端拾器建模是自动化仿真设计的重要环节,其准确性是保证各仿真系统模具干涉校验及曲线设计结果准准确性的前提。中国一汽工程技术团队在前期各项研发成果的基础上,自主开发了冲压端拾器自动设计技术,通过梳理端拾器建模流程,从端拾器建模准备模型建立、结果校验三个过程进行系统分析,形成了完整的端拾器自动建模技术的实现路径及开发方案。
该技术实现了三项行业技术突破,首次实现了多仿真环境下的整合。
三大仿真平台在同一环境下整合,7条红旗冲压线100%覆盖,首次实现冲压端拾器智能设计,将传统的手动装配升级为系统智能装配,消除了员工重复性工作,领先行业内平均建模效率百90%以上。首次实现端拾器搭建图纸自动关联生成功能,通过三维数据及二维图纸的交互和优化车型自动化生准周期10天以上。
第二个智慧场景是生产典型场景,涂装车序自适应管控技术。涂装车间因返修、双色导致车序兑现率低,是行业内每个主机厂都面临的问题,这直接导致了总装车序的混乱和物流运营成本的增加。
涂装团队创新开发了柔性智能车序管控技术。
一是规划全新工艺路线,构建车序自适应管控应用场景,通过创新算法识别涂装制造过程中车序变化,并自适应的调整,还原生产队列。
二是开发了集成输送、横移、旋转、举升等功能的智能AGV,按场景路径和算法指令进行了车身转运,打破传统的对每个立体库独立分区、分类的存储模式和调度模式,实现了涂装车间立体库无边界群控调度生产。
三是涂装车间全部产品基于实时库位和最短路径下的无边界存储和按需模式调度发车,最大程度的进行车序还原。
综合以上提升交付车序兑现率接近100%,降低物流运营成本每年达到1000余万元,物流操作岗位优化了60个。
第三个是智慧质量典型场景,焊点质量预测。
为了保证焊接质量的稳定性和可靠性,焊接团队通过焊点质量调控方法及相关边缘技术,创新开发了焊接质量预算预测技术,构建了模块化的质量预测方案。
该方案一是将深度学习应用应用于焊接质量的预测和诊断,通过适合多分支结构的深度神经网络模型构建和超参数探索等相结合,利用分层搜索实现最优超参数逐层冻结和逐层训练,建立了深度学习和自我优化的方法,实现了神经网络超参数的自主优化。
二是通过对机器人、焊机等设备加装先进的传感系统,并进行全面的联网,实时采集焊接过程中的参数,运用AI算法进行质量分析,实现焊点质量的在线实时诊断和预测。
这些预测数据及诊断结果作为质量管理能力中心的输入,为智慧决策提供数据积累。
一方面结合预测数据与焊接质量标准的智能分析,系统通过自决策实现对产线的智能控制,防止质量风险的扩大。
另一方面结合预测数据的动态监测及分析结果,为工程师系统优化焊接工艺提供了数据依据。
通过该场景的开发应用,实现焊接质量核心要素监控率达到了100%,GP稳定性提高了20%,提高了产品质量和生产效率的同时,也为制造工艺的改进和优化提供了新的载体和路径。
在论坛上,中国一汽党委常委、副总经理刘亦功表示:除了先进的智慧工厂,中国一汽将策划实施“旗帜创新工程”,加大新能源、智能网联领域技术攻关,抢占技术制高点,做深做透产业链;将以‘All in’新能源汽车的姿态,全域推动电动化转型,坚决打赢新能源汽车强势崛起攻坚战;将继续秉持“崭新独创、合作共赢”理念,突出高质量发展导向,实现创新能力的行业领先和世界先进,真正成为汽车产业原创技术策源地;将充分发挥企业创新主体作用,与行业同仁一道,为建设制造强国、汽车强国做出新的贡献。
为此,中国一汽在论坛邀请了多位国内知名院士,前瞻了汽车材料、制造技术、绿色智能技术的未来发展。
中国工程院丁文江院士做了题为《轻氢之镁,创新栽培》的前沿技术报告,中国工程院黄庆学院士的分享题目是《加强基础研究和产学研合作,推进高端装备自主创新》,中国工程院单忠德院士介绍了《绿色智能制造技术与装备发展》,中国工程院林君院士发表了《面向汽车制造产业的智能检测技术创新与展望》的精彩演讲,中国工程院谭建荣院士探讨了《智能机器人:从概念到产业》的前瞻话题。
在圆桌论坛环节,中国汽车工程学会会士、中国汽车工程学会汽车制造分会名誉主任委员、东风汽车集团有限公司原副总工程师邹恒琪主持了圆桌论坛,中国汽车工程学会副秘书长赵莲芳、中国汽车工业协会副秘书长何毅、中国汽车技术研究中心有限公司首席专家孟宪明博士等行业专家围绕“未来制造新范式”的主题进行了深入讨论,台上台下互动交流,共同探索未来汽车制造的发展方向。
会议同期,中国一汽还举办了先进制造技术成果展,秉持70年自主创新精神,从“制造”到“质造”再到“智造”发展历程的时空隧道。
大国工匠技艺展区,中国一汽荣获“大国工匠”称号的刘富强、齐嵩宇、杨永修等员工取得的先进成果展示;
智能智慧技术展区展示了焊装视觉智能定位技术、涂装车序自适应管控技术创新及应用、商用车轮胎自动随行装配系统等创新技术;
新能源技术展区的HEV电池壳一体化压铸技术、电机转子磁钢热固技术、商用车电机制造技术等备受瞩目;
在新材料技术展区,高韧性薄铝硅镀层热成形钢应用技术、镁合金车身结构件及动力总成产品技术开发及应用等同样极具吸引力;
数字化技术展区则有MEB底盘黑灯线、智能公差仿真探索与应用、工厂智能化能源管理等创新项目展示。
来自行业组织、科研院所、主机厂、零部件企业、装备供应商和媒体的700多位代表共享技术盛宴。